Top 10 Reasons Why AI Hiring is Reshaping the Manufacturing Industry’s Hiring Process
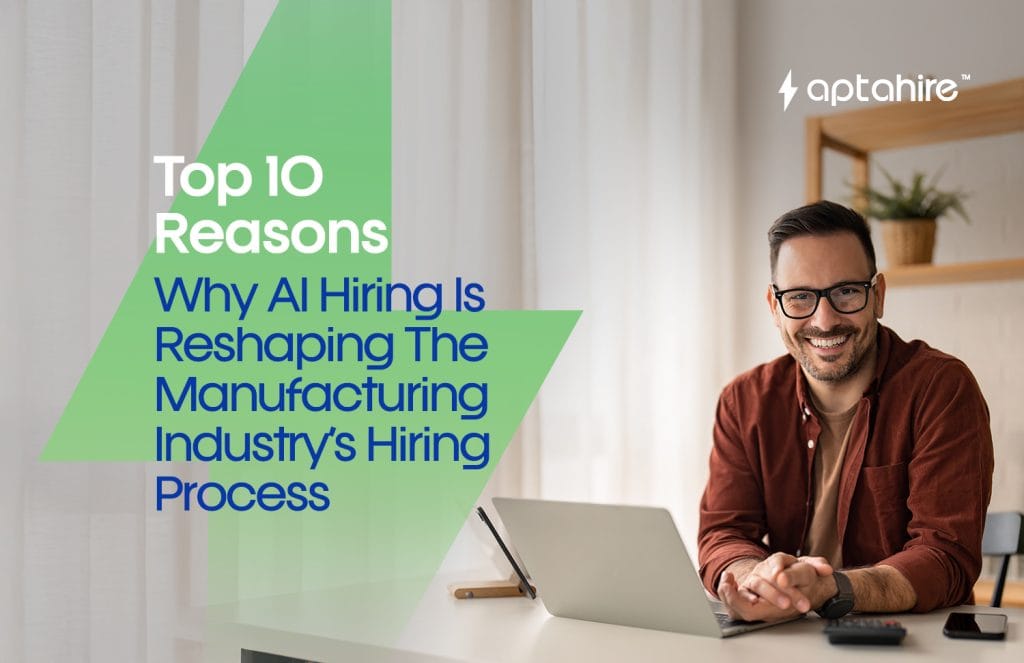
Introduction
The manufacturing industry has always been the backbone of global economies, but today, it’s undergoing a transformation that extends beyond robotics and automation on the production floor. One of the most significant yet less visible shifts is happening in the hiring process. As the sector faces talent shortages, rising operational complexities, and a push toward Industry 4.0, traditional recruitment methods are struggling to keep pace.
Now comes AI hiring, an evolution that’s not just optimizing how manufacturers find talent but fundamentally reshaping the entire process. From predictive analytics and skill assessments to AI-driven onboarding, manufacturing recruitment is getting smarter, faster, and more competitive.
Let’s dive deep into why AI hiring has become indispensable for the modern manufacturing workforce.
1. Accelerating Time-to-Hire for Critical Roles
Manufacturing often requires rapid hiring, especially for project-based contracts, seasonal surges, or unexpected production demands. Traditional hiring methods can take weeks, costing companies precious production time.
AI-based Applicant Tracking Systems (ATS) and predictive sourcing tools can slash hiring time by up to 50%, according to LinkedIn’s Global Talent Trends report. By automating resume screening, skill-matching, and interview scheduling, manufacturers can fill positions in days instead of weeks.
Tip: Implement AI-powered resume parsers to automatically match candidates to technical roles like CNC machinists, assembly line operators, or robotics technicians.
2. Precise Skills Matching with Machine Learning Models
Finding candidates with the exact combination of technical certifications, safety training, and practical experience can be challenging. AI uses machine learning algorithms to parse not just resumes, but also micro-credentials, portfolios, and even project histories.
For instance, if a manufacturing unit needs a welder with AWS D1.1 certification plus robotic welding experience, AI tools can instantly scan thousands of profiles and identify top matches, even those hidden in passive candidate pools.
Interesting Fact: AI models can analyze 10,000+ data points in under a second, including obscure certifications or niche experience in legacy machinery, often overlooked by human recruiters.
3. Enhancing Diversity and Reducing Bias
Manufacturing, historically dominated by a less diverse workforce, is now making deliberate moves toward inclusion. However, unconscious biases in hiring can be difficult to eliminate manually.
AI hiring platforms that are properly trained with bias-mitigation protocols ensure that candidates are assessed solely on skills, experience, and potential, not gender, race, or age.
Stat: A Harvard Business Review study showed that AI-based hiring tools can increase workforce diversity by up to 25% in industrial sectors.
Tip: Always select AI vendors who offer transparent bias-auditing and fairness reporting.
4. Predictive Analytics for Workforce Planning
AI hiring is not just about today’s needs; it’s about predicting tomorrow’s demands. By analyzing production forecasts, employee turnover rates, and seasonal trends, AI-driven workforce analytics can predict when and where hiring needs will spike.
For example, if data shows a consistent dip in CNC operators every Q3, manufacturers can proactively start sourcing in Q2, reducing operational disruptions.
Technical Insight: Predictive analytics platforms use regression analysis, time-series forecasting, and clustering algorithms to offer hiring recommendations months in advance.
5. Video Interviews Powered by Emotion and Micro expression Analysis
Manufacturing roles often require soft skills like attention to detail, resilience, and teamwork, traits hard to assess from resumes alone.
AI-driven video interviews can now evaluate facial micro expressions, tone modulation, and even eye movement to assess candidates’ honesty, confidence, and emotional intelligence.
Tip: Use AI-enhanced video interviews for roles requiring high safety compliance, such as forklift operators or chemical plant workers.
Interesting Fact: Studies show that micro expression analysis during interviews can improve selection accuracy by up to 22% compared to traditional interviews.
6. Seamless Onboarding through Intelligent Automation
Once a candidate is hired, the onboarding experience can make or break retention. Manufacturing environments demand quick integration, safety training, and role-specific certifications.
AI onboarding systems automate this entire journey, sending personalized training modules, setting up safety compliance courses, and integrating new hires into HRMS and payroll platforms without human intervention.
Stat: Companies with AI-automated onboarding processes see 82% faster employee productivity in their first month, according to a Deloitte report.
7. Real-Time Skill Gap Analysis
Manufacturing plants need dynamic teams who can adapt to technology shifts like IoT-driven equipment, smart factories, and robotics.
AI talent platforms continuously analyze existing workforce skills against future technology requirements, flagging gaps before they become bottlenecks.
Technical Detail: AI tools leverage Natural Language Processing (NLP) and Deep Learning to parse job descriptions, skills libraries, and employee profiles for real-time capability mapping.
8. Cost Reduction through Intelligent Hiring
High turnover rates, particularly in entry-level manufacturing roles, can cost companies millions annually. AI-driven recruitment reduces cost-per-hire by identifying candidates with longer tenure probabilities based on behavioral science algorithms.
Moreover, by automating repetitive administrative tasks, HR teams can focus on strategic initiatives like workforce planning and retention.
Stat: According to SHRM, AI hiring can reduce cost-per-hire by up to 30% in the manufacturing sector.
9. Enabling Hyperlocal Talent Acquisition
Large manufacturing companies often need to hire plants located in remote or rural areas. Traditional job postings often fail to attract enough qualified local talent.
AI-driven geofencing recruitment ads, micro-targeted social media campaigns, and local database mining ensure that the talent pool is not just large but relevant to plant locations.
Tip: Use AI geospatial analytics to identify workforce concentrations and create hyperlocal hiring campaigns.
10. Supporting Workforce Upskilling and Career Pathing
Modern manufacturing jobs require constant upskilling. AI hiring platforms now integrate Learning Management Systems (LMS) to assess candidate skill gaps during the hiring phase and suggest personalized upskilling paths post-hire.
This approach not only ensures immediate role fitment but also fosters long-term employee development, reducing attrition.
Interesting Fact: Companies using AI for hiring and upskilling see 50% higher employee retention rates in their manufacturing units.
Hire Smarter for the Manufacturing and Technology Industries with Aptahire
Aptahire, the AI-powered interviewing platform, is designed to streamline and strengthen the hiring process for manufacturing and technology companies. With bulk resume upload, automated screening, and interview scheduling, Aptahire simplifies high-volume recruitment without compromising precision. The platform conducts interviews through a smart AI Avatar, providing instant candidate feedback, detailed assessment reports for HR teams, and downloadable video records for review.
Its built-in personality tests measure candidates’ emotional intelligence alongside technical skills, while advanced cheat detection ensures interview authenticity. Aptahire’s multilingual support makes it ideal for diverse global teams, helping companies reach talent beyond language barriers.
Whether you are a small, mid-sized, or large enterprise, Aptahire adapts to your hiring scale with seamless integration, real-time insights, and intelligent analytics. By combining technology-driven efficiency with human-like assessment accuracy, Aptahire transforms how manufacturing and tech firms build high-performing, future-ready teams.
Final Thoughts
The manufacturing industry is at a crucial inflection point, transitioning from traditional operational models to smart, interconnected ecosystems.
AI hiring is no longer a futuristic luxury, it is a critical necessity for manufacturers aiming to build agile, skilled, and future-ready workforces.
By leveraging AI’s capabilities in predictive analytics, unbiased screening, skill mapping, and onboarding, manufacturing companies can dramatically enhance their recruitment outcomes while positioning themselves competitively in the industry 4.0 era.
However, successful AI hiring in manufacturing demands strategic implementation, including clean data, human oversight, ethical AI practices, and continuous optimization. Those who embrace this transformative shift now will lead the next generation of industrial success stories.
5 Common Mistakes to Avoid When Using AI Hiring in Manufacturing
- Using Outdated Data Models: Manufacturing technologies evolve fast. Outdated AI models lead to irrelevant candidate matching.
- Over-Relying on Automation: Always balance AI decisions with human judgment, especially for critical safety-sensitive roles.
- Neglecting Candidate Experience: AI-driven processes must still feel personalized to attract top talent.
- Ignoring Compliance Regulations: Manufacturing often involves stringent labor laws. Ensure your AI hiring platform is compliant.
- Failing to Upskill Recruiters: Your hiring managers must understand how to interpret and action AI insights correctly.
FAQs
1. How is AI improving the hiring process in the manufacturing industry?
AI automates resume screening, skill assessments, and candidate shortlisting, speeding up hiring while ensuring better matches for technical roles.
2. Why is AI important for manufacturing recruitment today?
The industry needs highly skilled workers quickly. AI helps by identifying qualified candidates faster, reducing hiring time, and minimizing skill gaps.
3. Can AI reduce bias in manufacturing hiring?
Yes, AI uses data-driven evaluations focused on skills and experience, minimizing unconscious bias and promoting diversity in manufacturing workplaces.
4. How does AI help assess technical skills in manufacturing candidates?
AI-powered assessments and video interviews can evaluate candidates’ technical expertise, problem-solving skills, and adaptability in real-time.
5. How does AI speed up large-scale hiring for factories?
AI can screen thousands of applications quickly, rank candidates, and automate interview scheduling, making mass recruitment efficient for manufacturing plants.
6. What role does AI play in onboarding manufacturing workers?
AI can streamline onboarding by automating document verification, training recommendations, and personalized induction plans based on employee profiles.
7. Can AI predict employee performance in manufacturing?
Yes, predictive analytics tools use past hiring data to forecast how a candidate will perform, helping manufacturers hire workers who stay longer and perform better.
8. Is AI cost-effective for manufacturing recruitment?
Absolutely. AI reduces recruitment costs by minimizing manual screening, improving hire quality, and reducing turnover, ultimately saving operational and training expenses.